Eliminating Hidden Factories Through Process Visualization
Mi Jin Oh| Sep 5 2023| 8 min read
Process mining, an essential method in the process visualization execution phase, enables a comprehensive understanding of business processes and facilitates the identification and resolution of issues like process delays and excessive ordering, addressing the challenges posed by hidden factories.
The Unseen Hidden Factory
When analyzing business processes through process mining, we often encounter “hidden processes” that are not documented in process definitions. This phenomenon is not limited to manufacturing companies; it also occurs in various industries. In the manufacturing context, these hidden processes are referred to as “Hidden Factories.” Hidden Factories are challenging to identify accurately, and they adversely affect production efficiency while increasing costs. Therefore, they must be promptly addressed and resolved.
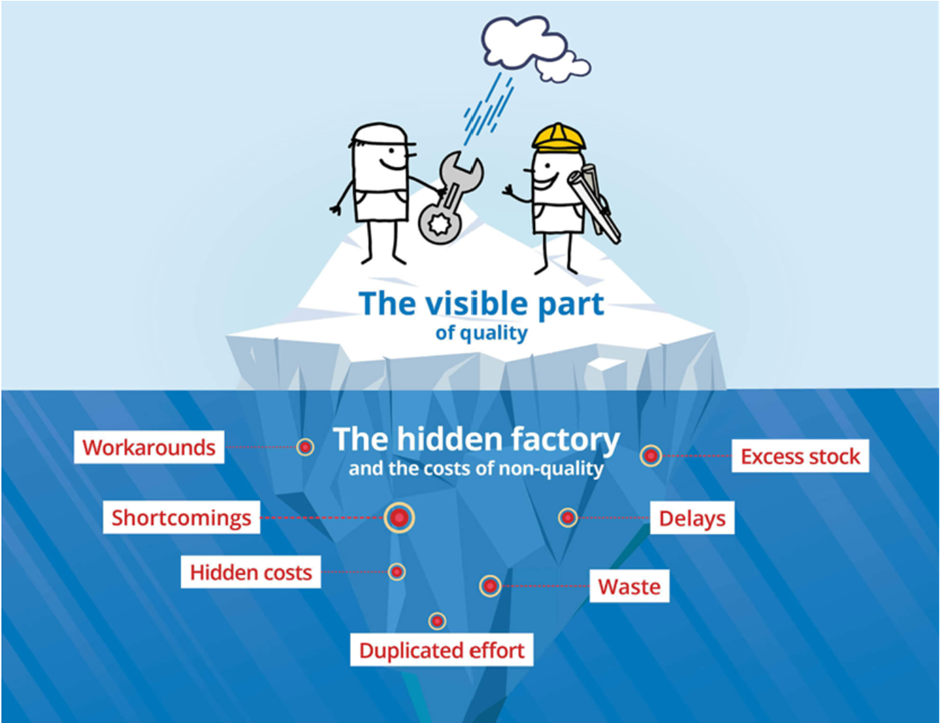
It’s theoretically natural for businesses to have a comprehensive grasp of their overall situation, but the reality often differs significantly. Achieving a holistic visualization of manufacturing activities is notably challenging and comes with significant investment requirements. Process mining, on the other hand, necessitates the enterprise’s existing IT systems without incurring additional infrastructure costs. It offers structural advantages that do not disrupt the operations of critical processes. Through this, hidden factories can be identified and eliminated.
Achieving with Process Visualization
Both Supply Chain Management (SCM) and Manufacturing Execution Systems (MES) in manufacturing companies contain data related to production schedules. Therefore, by analyzing event logs extracted from these systems through process mining, it becomes easy to identify how issues arising from inventory management can lead to production delays and more.
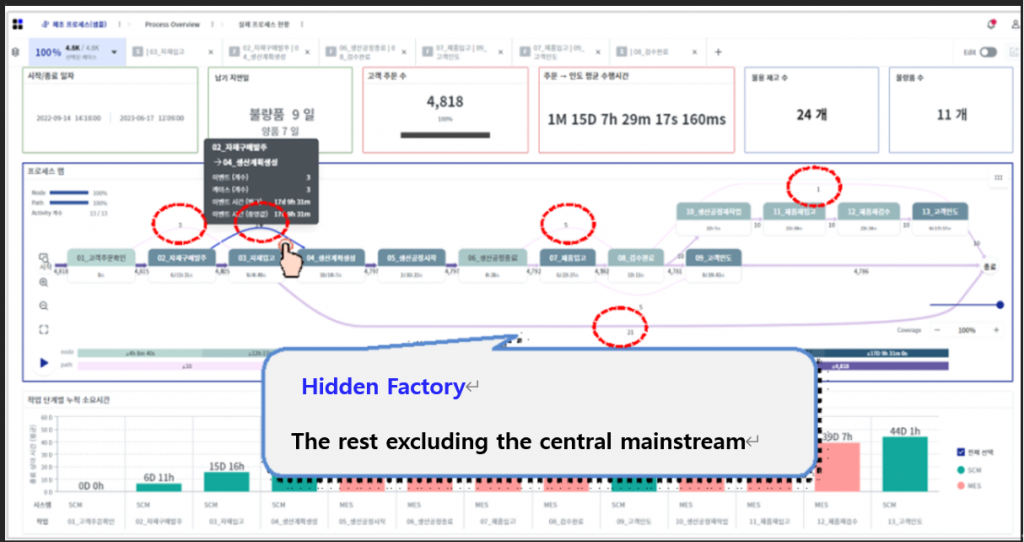
Sure, let’s look at an example. Company A, which produces automotive parts, has the following concerns in its major departments:
- Purchasing Team: They want to reduce inventory management costs.
- Production Team: They aim to identify bottlenecks causing production delays.
- Production Management Team: They seek to enhance production process speed through gap reduction.
- Sales Team: They wish to predict product delivery dates to meet customer commitments.
- Marketing Team: They want to promote products by understanding changing customer demands.
However, many companies struggle to address these concerns early or accept them as inevitable, ultimately leading to reduced efficiency in manufacturing companies. Process mining is highly effective in addressing and resolving these challenges.
In the previous article, we discussed the need for process visualization in the manufacturing industry. In this session, we will explore how to create an integrated perspective of processes, from procurement and production to sales and marketing, using log data from manufacturing companies. We will also delve into how to uncover hidden processes.
The Moments Requiring Management
In the manufacturing industry, there are three critical moments: the deadline for customer orders, the completion of ordered products, and the delivery of products to customers. It’s essential to minimize the time gaps between these moments to ensure the delivery of high-quality products to customers and achieve customer satisfaction.
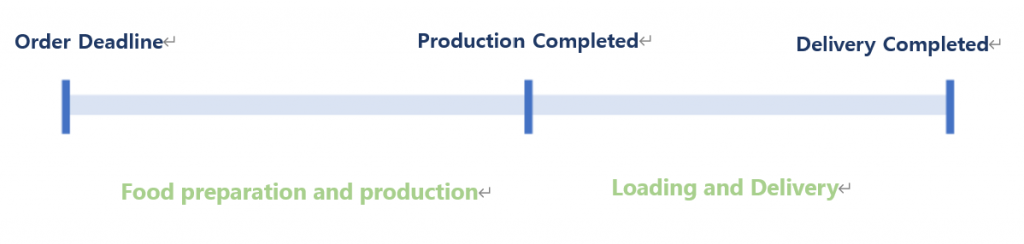
Why is the live cooking corner in buffets so popular? The answer lies in the graph. Three key moments almost happen simultaneously. First, there is no time gap between production completion and delivery completion since the food goes straight to the table when it’s ready. Second, there’s no order deadline. Chefs accommodate customer requests on the spot. This principle is a common concern for every company in the real world with customers.
Earlier, Company A, which manufactures automotive parts, also shares a similar concern. While the specifics may vary by department, the ultimate goal is to efficiently manage the three critical moments mentioned above to reduce overall lead time. Let’s explore how these concerns can be addressed using ProDiscovery.
[Purchasing Team] “We want to reduce inventory management costs.”
▶[Solution]
Optimizing the necessary inventory items and quantities to be held enables a reduction in obsolete inventory and overall inventory management costs, as well as a decrease in production downtime.
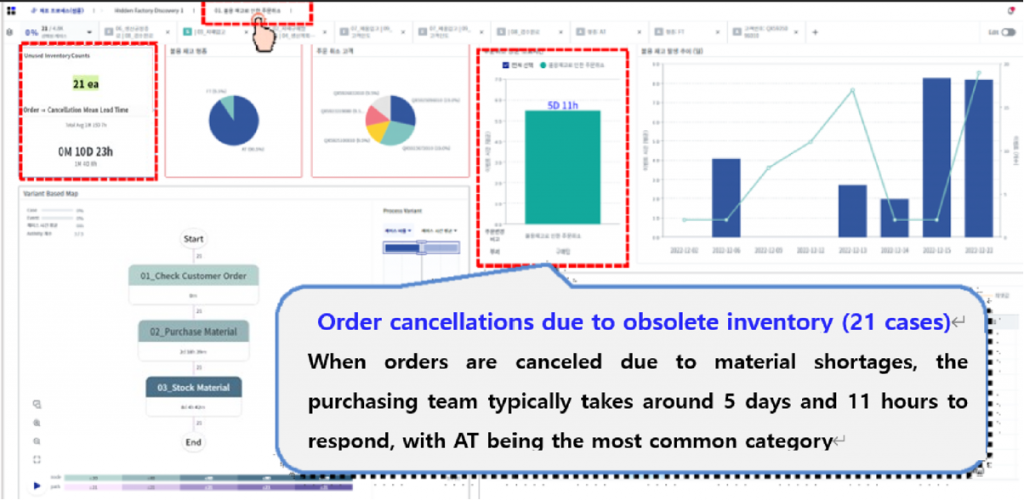
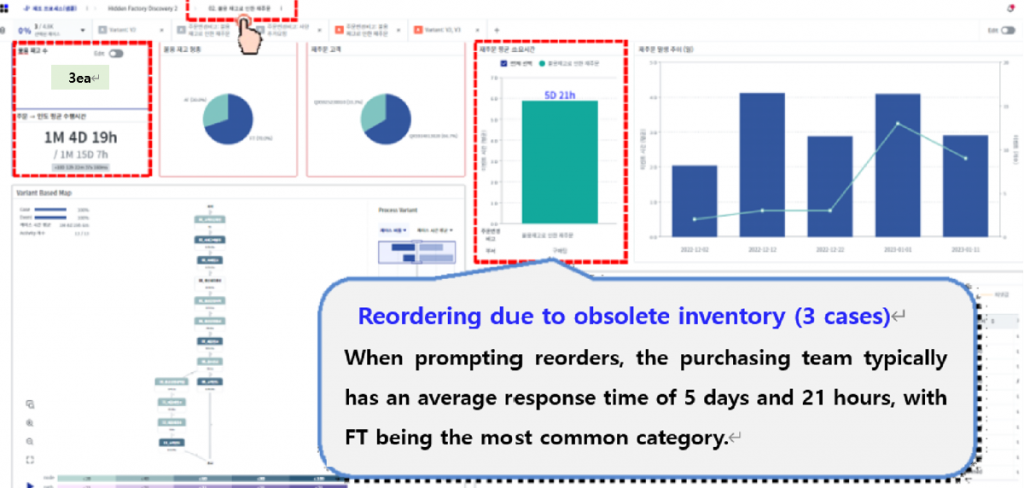
[Production Team] Identifying bottlenecks causing production delays
▶[Solution] Identifying when, at which stage, and why bottlenecks occurred to improve production efficiency and reduce defects
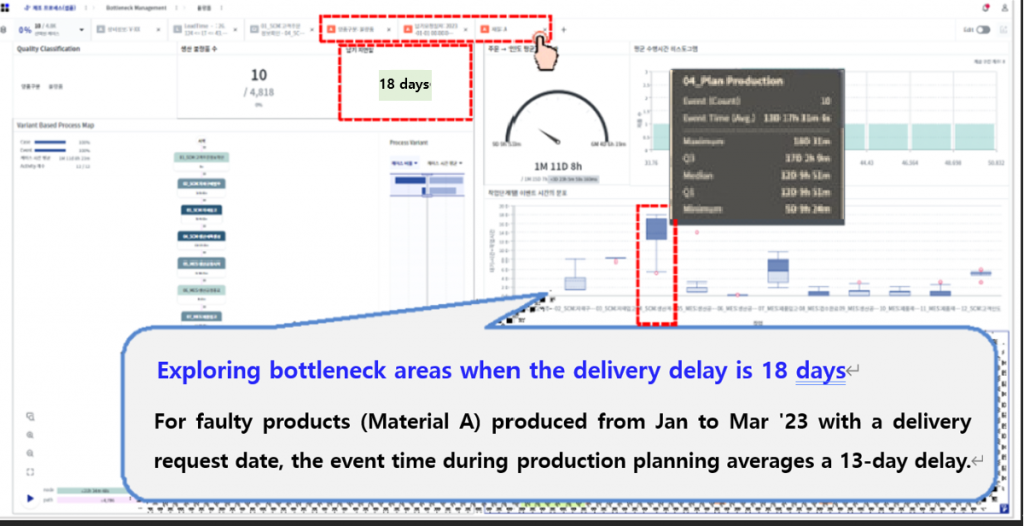
[Production Management Team] Want to improve production process speed by closing the gaps.
▶[Solution] Identifying when and where the gaps between planning and actual performance mainly occur is possible. Eliminating production process gaps leads to three benefits: first, product quality improvement; second, reduced machine downtime; and third, improved production process performance and efficiency.
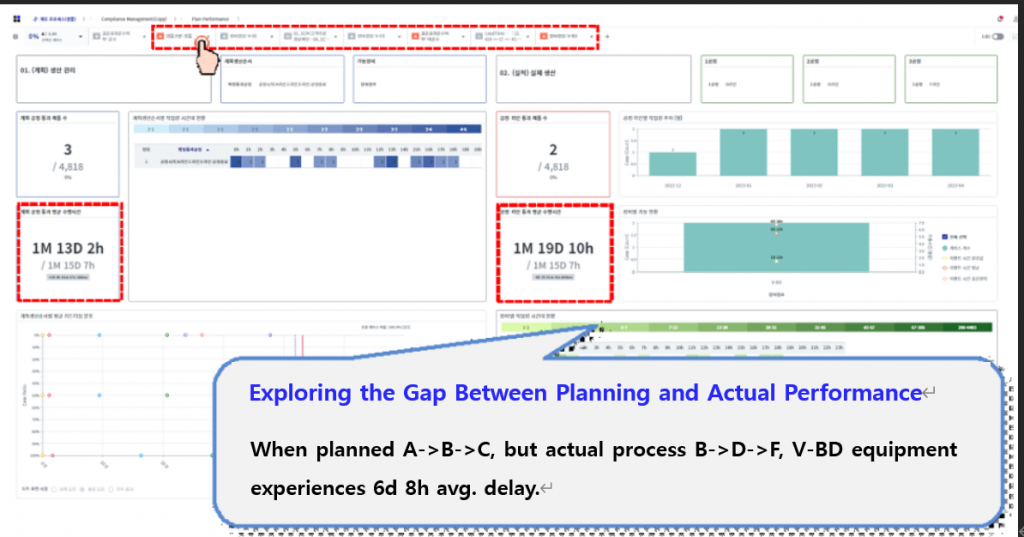
[Marketing] We want to understand changing customer demands and promote our products accordingly.
▶ [Solution] By segmenting customer patterns through portals, we can detect new technical requirements early and adjust promotion priorities based on the customer’s value contribution.
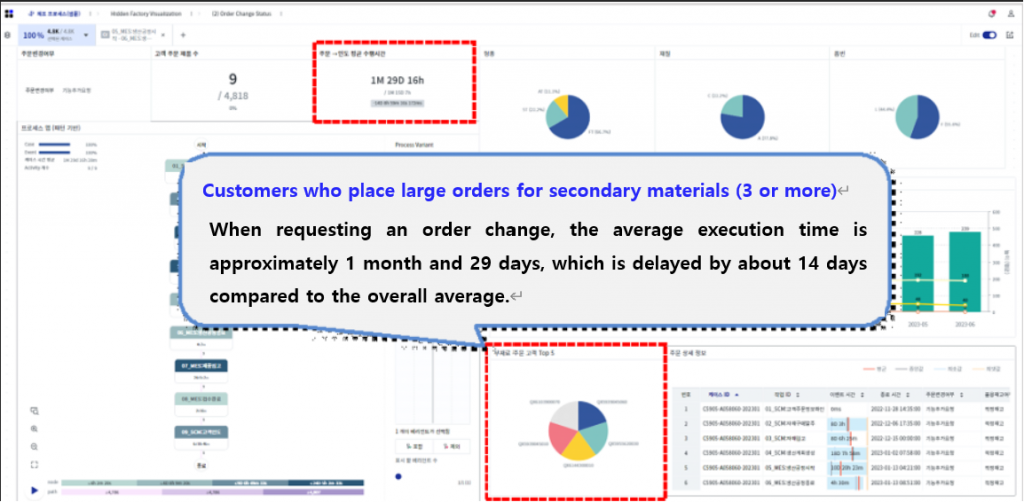
[Sales] I want to predict the delivery date of products to meet delivery commitments.
▶[Solution] Precise analysis of material replacement costs, factory downtime delays, etc., can provide quantitative evidence for optimal delivery date prediction.
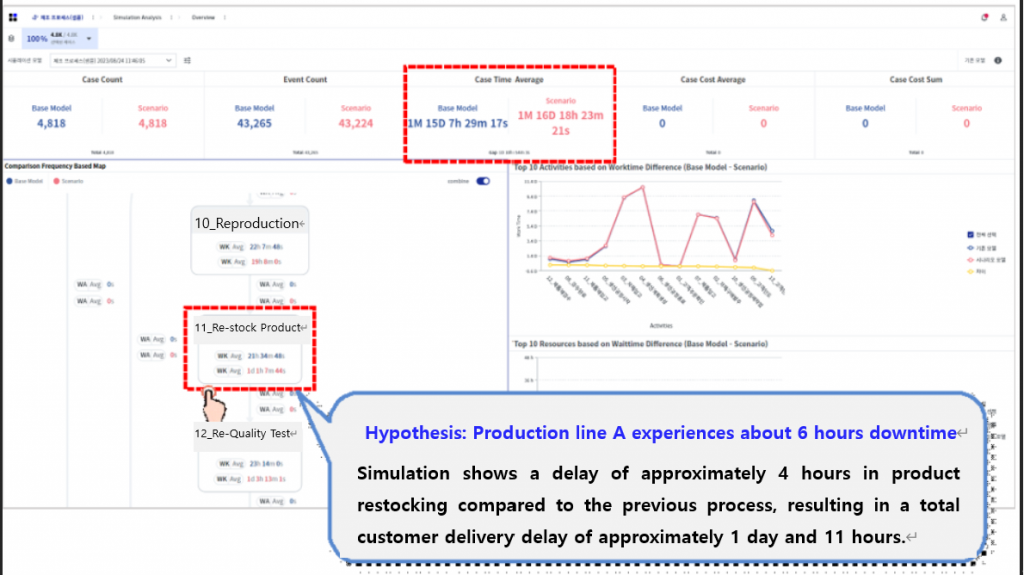
In the process of discarding, we finally see things
In the process visualization execution phase, the necessary method is process mining. It is a way to grasp the essence of business processes and find issues for improvement. In other words, it is the solution needed to accurately identify and resolve problems such as process delays and excessive ordering that support the hidden factories mentioned earlier.
- [Marketing] Tracking and managing the process of customers reviewing general information (orders, production, changes, etc.)
- [Purchase] Tracking and managing the process of materials moving from the warehouse to the production line
- [Production] Tracking and managing the process of components being applied to the final product
- [Sales] Tracking and managing the process of delivering manufactured products to customer